Keith Monks
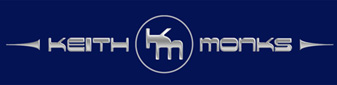
The 1960s was a time when great things were happening in British audio - and none more so than in Berkshire, England. A gentleman named Frank Ockenden was developing the Mercury Contact PickUp Arm. His friend John Wright was a consultant on PU arms & cartridges and wrote for various audio publications. He and Mike Beville, another engineer and businessman, formed a company called Audio & Design to put their ideas into practice.
Meanwhile Percy Wilson, technical editor of The Gramophone magazine, had been working for some years on ways to ‘properly’ clean records. Percy was already a legend in the audio industry: a pioneer of audio theory and design, and lifelong champion of electric sound reproduction as far back as the 1920s, he pretty much invented the modern pickup arm design which has been used by almost every arm and turntable manufacturer ever since.
Percy had previously introduced the original concept of record cleaning in his definitive book, The Gramophone Handbook (Methuen 1957) in which he suggested a rather surprising method, applying a mixture of lubricating oil and vinegar followed by washing in soapy water, rinsing with tap water, drying with a flannel, treating with antistatic liquid and running through several times with a Dust Bug. Percy enthused that the method “though rather tiresome, should prove effective.”
Still, it was a start and, realising the need to rethink his original approach for what now seem fairly obvious reasons, eight years and much further deliberating resulted in Percy’s first AES paper on the subject, "Record Contamination: Causes and Cure" (Audio Engineering Society, April 1965). You’ll read elsewhere on the internet about how this paper apparently describes a design for a record cleaner, but in fact it offers only tantalising hints about its construction, preferring instead to concentrate on detailing the various forms of external contaminants that compromise the sound of a record, and the problems associated with their conventional removal by simply dusting them off with a dry cloth - or, worse still, a wet one. A full description of the ‘cure’ of the title was, it was said, still “work in progress”.
Readers didn’t have to wait long though. By then Percy was already working on several working prototypes of devices which could solve these problems. One was the “Record Player Cleaner”, an outrageous and fascinatingly unlikely gadget which it was proposed could be mounted directly in front of the pickup cartridge on an existing turntable, with a forward facing brush to scoop up particles in the groove and an overhead tube to then vacuum them away before they reached the stylus.
The other solution was a proposal for a separate machine dedicated to washing a record and then drying it afterwards. Christened the ‘Record Doctor’, this machine was a laboratory prototype and big enough to fill a sideboard. It employed four different devices to clean the record – a liquid applicator, groove scrubber, ‘suction mop’ (an arrangement of tubes complete with rayon ‘lips’ supporting a standard cigarette filter !) and spinning brush for “final drying and polishing”. Ingenious, indeed revolutionary… and, despite rumours to the contrary, nothing like any record cleaner you’ll have ever seen since. Huge, fiendishly complicated in operation, and clearly impossible to manufacture (after all, in those simpler days the intention of its creator was to prove the scientific principle rather than satisfy a desire to profit from it). Nevertheless the ‘Record Doctor’ is historic: the first ever electric device for cleaning records.
Even back then though, and irrespective of the development history that followed, the importance of having separate built-in ‘wash’ and ‘dry’ devices built into the mechanism itself was considered a significant feature, and makes this first prototype the direct forerunner of what became the Keith Monks Record Cleaning Machine.
The ‘Record Doctor’ was presented to the Audio Engineering Society in New York in October 1965 along with Percy’s accompanying paper "Instruments For Record Cleaning" (Audio Engineering Society, also October 1965), and both received massive acclaim. Percy had once again come up with a ‘first’. The same prototype apparently went on be exhibited at the legendary Buxton hi-fi show where it has, thanks to the internet, gained almost mythical status – this may or may not have actually happened, as there’s conflicting information about it. But no matter: as for this prototype’s evolution into what would recognisably become a record cleaner, it was going to take another team of ingenious pioneers to make that happen.
This marvellous contraption caught the imagination of Audio and Design. John Wright had been writing for various publications including The Gramophone, and had become close friends with Percy. John suggested that they collaborate on developing Percy’s prototype into a product that could be built and sold. Percy agreed to become a consultant on the project.
It was at this point that John and Mike asked Pete Keeley to come onboard the record cleaning project. Pete’s engineering expertise had already produced a large speaker monitoring system for Audio & Design using Ted Jordan’s Titanium drive units. These monitoring systems were originally built for ATV Elstree and were produced at Pete's company Keesonic. Pete was (and still is) considered ‘the man that makes things happen’, and he was given the unenviable task of taking Percy’s theoretical concepts and turning them into reality.
‘pickup arm’ style mechanismMany months of discussions followed, firstly with Percy and then between the team in-house. Eventually it was decided that a ‘pickup arm’ style mechanism was the best way to replace Percy’s original cantilever and transverse motor drive for his ‘suction mop’. As Frank Ockenden was producing parts for the Mercury arm, all agreed he was the perfect candidate within the team to undertake research into building a new arm for vacuuming liquid off a record. Over the next few months Frank refined his ideas and hand built a pickup style arm with adjustable counterweight for testing and evaluation. Percy’s ‘suction mop’ of cigarette filter and rayon ‘lips’ were replaced by a soft plastic nozzle milled into a precise shape. This was the first time a pickup arm was ever used for record cleaning.
The next requirement was the turntable. Several Lenco turntable assemblies, an industry standard at the time, were acquired by Pete Keeley. He stripped and laminated the deck with formica to make it ready for the development parts. Assembly began, the original varispeed turntable motor was evaluated and retained, and Frank’s new arm was fitted.
Work then commenced on the washing section. A tried and tested brush for cleaning records was already available from Cecil Watts as part of his famous Parastat handheld cleaning device. Pete crafted a pillar and support arm which would hold the soft brush, spread the liquid and scrub the disc.
It was then decided that building the fluid application system into the unit would be essential especially if the machine was going to be used continuously (don’t forget the Machine was originally developed with record libraries like the BBC in mind). So a pump of some kind was needed to apply the liquid to the brush. A Delco car windscreen/windshield washer handpump was sourced which worked well, and this was fitted to the turntable deck.
Finally, the suction pump. Having considered and quickly rejected the idea of a standard vacuum cleaner motor on the grounds of noise, overheating and doubts about the wisdom of sucking moisture into a brush motor, another type of device was required (a decision about which most other makes of record cleaners that have come along since seem to disagree). Enquiries led to a British company making diaphragm pumps for laboratory and medical equipment. Samples were obtained, and these were fitted and tubed to the suction arm via a waste jar which would collect the spent fluid.
Final preparations commenced. The vacuum direction – from the inside outwards – had already been decided to follow the centrifugal force of the fluid as the turntable revolved. The scan time of the suction arm was calculated, a drive motor and suitable belt obtained, and a pulley arrangement devised and made. To synchronise with this system, and to follow Percy’s original suggestion of a fast rotation to minimise evaporation and recontamination from airborne particles, the turntable speed was set at 80 RPM. A switching system was devised to activate the various components for the ‘wash’ and ‘dry’ cycles, and at his speaker workshop Pete started work on building the first cabinet (it was evidently rather large).
The ‘No.1 RCM Prototype’ All the parts were fitted into the cabinet. The ‘No.1 RCM Prototype’ was ready for test. The first few cleans quickly revealed the pump needed a sprung base board to check vibration on the top deck. Tests then revealed that the suction nozzle, although soft, was still sometimes marking the records. Furthermore, the vacuum process was often intermittent, leaving traces of liquid behind. Various methods were tried before they eventually came up with the solution.
The true origin of the thread and nozzle arrangement of what has become the ‘Monks Method’ can now be revealed: Pete and Frank devised a system using a reel of special soft nylon thread, feeding out and running up inside the nozzle tip from below it. This minimised contact between nozzle and record, and ensured a small space between the two in which an intense concentration of suction could be created.
To stop recontamination or marking of the record, it was decided that the piece of thread touching the disc should be constantly refreshed. A reel holder was devised and fitted inside the unit and, connected to this assembly, a motor running slowly in reverse reeled out the thread so, with every scan of the arm, the thread would be replaced. The force of the suction would then carry the used thread away with the dirty fluid.
The system was completed with a thin brass tube inserted through the suction arm to carry the clean thread to the suction nozzle in the arm head. This ran alongside the plastic tube carrying the spent thread along with the used fluid back down to the waste jar.
The markings disappeared. The space made by the thread made the suction capability of the system increase dramatically, leaving the records completely dry. The prototype was now complete. A diaphragm pump, a pickup style arm, and a soft plastic nozzle with a concentrated suction suspended off the record by a thread - the very first time a record cleaning system used this method was for the Keith Monks Record Cleaning Machine.
The ‘No.1 RCM Prototype’ The following months were spent on further checks and tests, with minor modifications made along the way. Then, at last, Pete and Frank decided they could do no more; the prototype was finished. By now it was 1968, nearly two years after the project began, and the time had finally come for their ‘new baby’ to be shown to the man that started it all. Audio and Design rolled out the red carpet, and Percy Wilson was invited over to inspect their work. Percy spent a long time with the two engineers, sharing experiences and going through each aspect of the machine in detail. At the end of the day, he declared that it had been a long journey for them all to get to this, an operational machine. And, with a little more work, he now believed that A&D had the makings of a saleable product. The team went home elated and no doubt satisfied with a long job very well done.
John Wright and Mike Beville, now eager to recoup their investment in the r&d, were turning their attention to the sales and marketing and had already taken on a new sales manager, one Keith Monks. Keith had worked for several tape recorder companies and had built up a good relationship with a number of dealers and broadcast companies. Back at Keesonic Pete Keeley was working on the cosmetics, including the angled front panel that has since become the distinctive signature style of the KMAL Machine, and finalised the basic layout you still see today. Pete’s team were now ready to put the first Record Cleaning Machines into production. Five pre-production units were built, and the team prepared to concentrate their efforts on the biggest prize in European broadcasting: the BBC.
At that time the BBC were rolling out an expanding number of stations broadcasting in stereo on the VHF (FM) band, and the quality of the medium demanded new heights in quality, clarity, and minimal noise. Since the medium not only made the music sound better but also showed up every flaw, and as most of their broadcast output was on disc, so it was becoming absolutely imperative that the BBC’s records sounded their best. For A&D, they needed the sort of shot in the arm only possible from a large client with deep pockets. The interest and support of the BBC was therefore going to be vital in getting the RCM off the ground. Some priming had been going on along the way to whet their appetites, until finally Keith had the prototype in his hands and was able to book an appointment with the Head of Audio Engineering at Broadcasting House. The weekend before the meeting, he took the Machine home together with all the plans, and started work on the costings about which the customer would no doubt be interested…
All looked rosy… but then without warning, disaster! The following Monday morning in early January 1969, Keith turned up for work as usual, only to find the place shut up. After waiting several hours, he returned home. That evening, he received a phone call from (we think) Mike: Audio and Design, having invested so heavily in the development of so many long-term projects including the aforementioned Mercury Pickup Arm and the titanium cone speakers as well as the RCM, had been running short of money. In the end it took just two large customers to withhold payment, the bank withdrew their support, and A&D were forced to close. On the eve of what would surely have been their biggest success to date: five days before the meeting that Keith had arranged with the BBC !
This left Keith with something of a dilemma: should he go ahead anyway and court his new, highly important contacts who were already enthused by the idea of this revolutionary piece of equipment? Or should he throw in the towel, tell them the bad news and wander off into the (winter) sunset? Well, Mr Monks was nothing if not resourceful – he kept the appointment. And came away with a letter of intent for three Machines.
There followed what must have been a rather frantic few days. John and Mike, no longer in a position to contribute but presumably unwilling to see their latest recruit starve, steered the way for Keith to buy the rights to the RCM from the liquidators. Pete Keeley agreed to work with Keith on the same arrangement he had set up with A&D – Keesonic would build them while Keith’s company would now market them - which meant the production facility and expertise were secure. Finally, Keith struck lucky with the bank: the local business manager turned out to be a hi-fi enthusiast ! Keith Monks Audio was up and running.
Keith took these first three ‘production’ Machines up to the BBC in London, and there they underwent a considerable amount of testing. At the end of the tests, bar a few minor recommendations to meet BBC standards, the engineers declared themselves impressed beyond even their expectations (and, since BBC engineers are expected to be strictly impartial, this was high praise indeed). So much so in fact that the Head of BBC Radio Engineering called a meeting with the BBC Governors - I believe this was sometime around summer 1969 - and invited Keith to demonstrate a Machine to the assembled group of VIPs. Keith came away with another order for the BBC – his first of many – and there started a long and fruitful association between the two organisations which continues to this day.
Word spread and interest soon picked up - in fact the only problem Keith had was having to carry the outsize unit - then even bigger than it is today - to show to stations, dealers and exhibitions around the country. So Pete built him a two-box unit with the turntable and deck components in one box and the vacuum pump in the other, with tubes and cables linking the two. Two smaller, lighter boxes made it easier to transport an RCM, set it up and show off the different principles and their associated components. Keith Monks Audio was able to claim yet another first - the world's first two-box Record Cleaning Machine.
Prototype work carried out on the RCM 1969Pete Keeley’s team could at last commence full production of the RCM, only now for Keith Monks Audio Limited (or ‘KMAL’ as the equipment badges were by now displaying), and this arrangement continued for several more years. By the early 1970s the fortunes of both companies were looking up, but this presented a new set of challenges. Keesonic’s speakers were becoming more and more popular, and demand for the Record Cleaning Machine was starting to take off with interest from Europe at the Hanover Fair spilling over into inquiries from the States and even the Far East. The time had come and the decision made: Keith moved his business out of the family home and into premises, a factory unit in his home town of Fleet in Hampshire. New engineers were trained, and Keith Monks Audio took over the manufacture of the Record Cleaning Machine in-house.
The rest of the story is well documented elsewhere. Keesonic went on to become a major player in the UK industry in the 1970s, manufacturing speakers including the famous Keesonic ‘Kub’ as well as working on ‘concept’ products for EMI, Plessey and Boots amongst many others. It is a little known fact that Keesonic also co-developed and built the legendary KMAL ‘Elf’ range of bookshelf speakers for Keith Monks which won a number of awards and became hi-fi bestsellers throughout the 1970s.
A special silver Record Cleaning Machine was presented to the Queen for her Silver Jubilee in 1977And Keith Monks Audio became one of the most famous audio accessories manufacturers in the world, with Keith going on to launch a myriad of products in first hi-fi and later professional audio (more on this in the Keith Monks section). His wife Sheila joined the business to run the office and ‘keep the boss in order’. Sales grew throughout the 1970s and by the 1980s the Machine was in use at most major radio stations worldwide, while every major city around the world boasted at least one KMAL dealer. A special silver Record Cleaning Machine was presented to the Queen for her Silver Jubilee in 1977, with both Keith and Sheila summoned to Buckingham Palace to demonstrate the RCM to an apparently delighted Prince Charles. And the decade culminated in the opening of Keith Monks USA in New England, an award for Audio Excellence from the AES, and The Absolute Sound awarding the Keith Monks Record Cleaning Machine their coveted award for ‘Audio Accessory of the Decade’.
Links with the BBC continued. As well as developing a number of key products with BBC engineers, most notably the LS1/8 powered monitor loudspeaker (an active version of KMAL’s famous ‘Elf’ hi-fi speaker), from 1970 onwards the BBC’s main Central Record Libraries, the BBC Archives Library, the BBC World Service, the BBC Transcription Service, as well as regional and overseas stations with sizeable collections all took delivery of a Monks RCM, with an instruction that every record kept by the BBC was to be cleaned on the Monks prior to broadcast, a routine which we understand is still adhered to today.
Following the success of the Keith Monks, a number of budget cleaners started appearing in the 1980s, but all went for a cheaper technique and the KMAL Machine continued to thrive. Eldest son Jonathan joined the firm having spent a few years first ‘finding his feet’ in several electronics companies. The advent of CDs soon after started to marginalized demand for records, but not before a late flurry of activity in the late 1980s and a renewed marketing drive orchestrated by Jonathan and directed at the many broadcast companies, who bought KMAL RCMs to make their record collections pristine before archiving them to digital, usually at that time onto DAT.
By the early 1990s the late boom had dwindled to a trickle, and Keith decided the time was right for a quieter life in the South West of England that he and Sheila had always promised themselves. But the Record Cleaning Machine wasn’t quite out of his system yet. Keith closed the factory and, on moving to Cornwall, set up an engineer in his backroom and together they built and sold the Machine ‘cottage industry’ style right up to his death in 2005. During this time some notable customers were added to the roll of honour including the British Library, the US Library of Congress and Harrods in London. What followed is all detailed elsewhere on this site – Jonathan’s relaunch as keith Monks Audio Works
, the move back into full factory production with a new 2000sq.ft production facility, and the opening of a new Keith Monks America (again in New England) - bringing history full-circle and the story right up to date.
Keith Monks. “Making records sound better since 1969.”So, there you have the true story of record cleaning - or, at least, the bare bones of it. Some of the documentation is a little hazy here and there it must be said, and there are a few gaps I would be delighted to fill. I see this as a part of the site that will continually evolve – in some ways because I’d like to think that our new operation is in some small way contributing to history still being made.
Anyway, please feel free to contact me with additions and amendments - all contributions are gratefully received, and I’m still in contact with the few major characters that are still with us and who have helped piece the story together. I would like to give particular special thanks to Pete Keeley for his valuable contributions to this section and, with history coming full circle yet again, for his invaluable advice and experience in general over the years - first to my father, and now to myself.
Keith Monks. “Making records sound better since 1969.”
Hinweis zu Aktualisierungen Ihrer Keith Monks-Produkte:
Auf dieser Webseite finden Sie den Produkt-Support und weitere Informationen zu Keith Monks-Produkten: